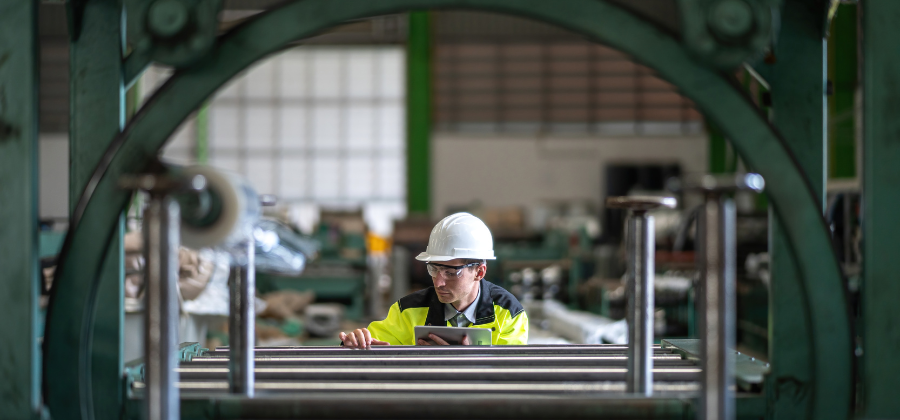
Manufacturers today continue to face ongoing uncertainty such as fluctuating demand, supply chain disruptions, and technological challenges. According to a recent study from Deloitte, technology is poised to play a significant role in supporting manufacturers in taking on the challenges they could face this year. With smart factory advancements and continuous hype around the values of generative AI, it’s more crucial than ever that manufacturers look to stay ahead of the curve.
To remain agile, leading manufacturers choose Spotfire® analytics. Spotfire is a visual data science platform that makes smart people even smarter by solving complex manufacturing problems to reduce costs, improve operations, and increase profitability. Getting the right insights at each stage determines profitability and success for your organization. Learn more in this blog about the three key ways Spotfire can make your smart factory even smarter.
Mitigate risk and improve yield with anomaly detection
What are anomalies, and why do they matter? Anomalies can manifest as sudden spikes, dips, or fluctuations of parameters like temperature, pressure, vibration, or energy consumption. They may indicate equipment malfunction, material defects, or other issues that could impact product quality or production efficiency. If your smart factory doesn’t keep track of anomalies, it could result in lower product yield and quality over time.
While anomaly detection is key to success, it’s not always easy. Manufacturing processes often generate large volumes of complex and heterogeneous data, making it challenging to preprocess and analyze effectively. Additionally, it requires the right skills. Distinguishing between normal distributions and genuine anomalies can be difficult, requiring robust algorithms capable of identifying subtle deviations while minimizing false positives. And implementing real-time anomaly detection systems requires efficient data collection, processing, and communication infrastructure, which can be challenging to set up. This is where Spotfire can help.
Spotfire allows operations managers, quality assurance engineers, data engineers, and data scientists to create custom visualizations—or plug-and-play data science components—that suit your specific needs. These custom visualizations or data science components can be shared and managed in the Spotfire library as reusable, pluggable assets. Nontechnical Spotfire users can use these components as building blocks to quickly construct analytics apps for their specific needs.
With Spotfire extensions, you can use anomaly detection to optimize your production efficiency and prevent costly failures—ultimately mitigating your overall risk and improving yield. Learn more about anomaly detection in this ultimate guide.
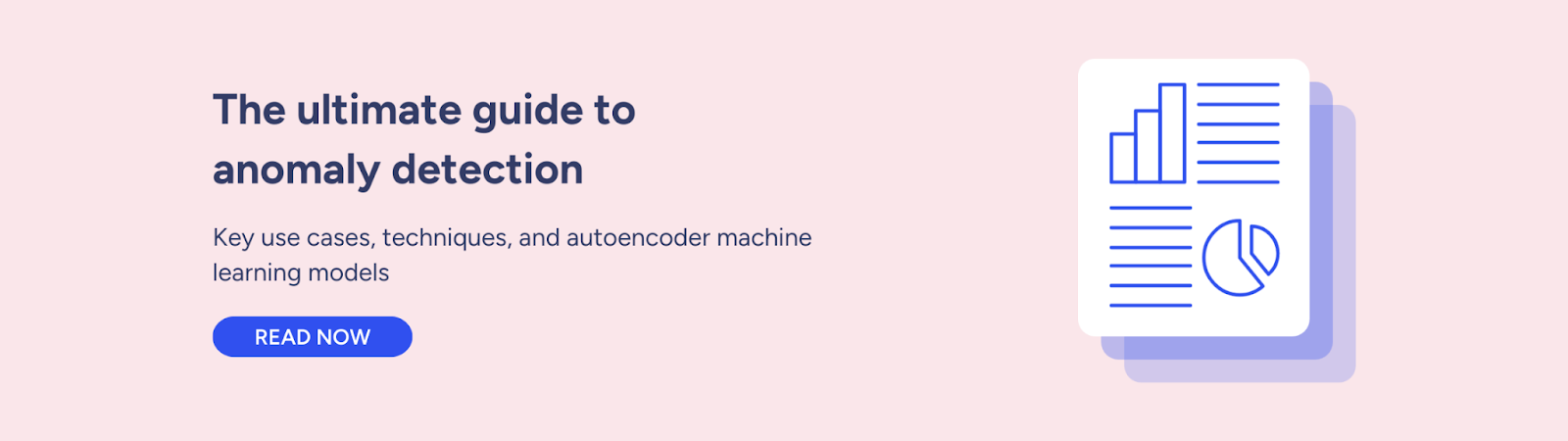
Minimize downtime with predictive maintenance
Predictive maintenance is more than just knowing when your machines need repairs. It’s about creating a factory that is always on and always optimized. When your machines are running at the peak of performance, you can operate more efficiently, reduce downtime costs, and maintain product quality. With predictive, data-driven insights into your equipment, your company can maintain a competitive edge in the market.
If creating a resilient factory was simple, all companies would do it. However, implementing predictive maintenance systems requires access to pre-processed, high-quality, and real-time data from sensors and other sources. Data is key to creating predictive models. Developing accurate models relies on historical data, which may be limited or incomplete. The final challenge is that interpreting the output of predictive maintenance algorithms and determining the appropriate maintenance actions can be complex. Acting on insights correctly requires collaboration between data scientists, engineers, and line-of-business knowledge workers.
To overcome these challenges, manufacturers partner with Spotfire. Spotfire analytics can connect to any data source and process data in real time, applying statistical models on incoming data. This not only allows manufacturers to process a larger amount of data but also allows them to detect anomalies as soon as they occur. Spotfire offers AI-recommended interactive visualizations and data preparation features that allow users to immerse themselves in the data and uncover the unknown. You can dig deep into your data at the speed of thought by leveraging the AI-driven, drill-down capabilities that let you uncover the hidden patterns in your data.
Spotfire allows users with ranging technical skills to collaborate effectively. This is made possible because Spotfire allows you to compose highly interactive Analytics Apps that are business-friendly. These apps can easily be designed using reusable pluggable building blocks that perform sophisticated algorithms prepared by data engineers or scientists.
Learn more about how Spotfire empowers predictive maintenance. Discover demos and real use cases in action.
Gain insights into product performance with field patterns and defect classifications
With valuable insights at your fingertips, you can drill into product performance, processes, and the root causes of failures. With accurate defect classifications in place, you can identify areas for improvement and take proactive measures to enhance product quality, reliability, and customer satisfaction.
Data might stand in the way of your product performance. Collecting and organizing data from diverse data sources—including sensor data, quality control records, and maintenance logs—can be complex and time-consuming. You’ll also need the right expertise to develop robust algorithms capable of accurately detecting and classifying fail patterns and defects, preferably an expert in data analytics and machine learning. And you won’t just need data experts—interpreting the analysis and translating it into actionable insights requires collaboration between data scientists, engineers, and quality control experts.
Spotfire is scalable and flexible to help you master these issues, allowing you to adapt to changing business needs and scale fail pattern and defect classification initiatives as your operations grow. Spotfire analytics leverages machine learning algorithms and predictive modeling techniques to identify patterns, trends, and correlations in data related to product failures and defects. This technology gives you accurate information to make informed decisions to improve production yield.
Check out this demo on Wafermap Pattern Recognition, which uses classification techniques to identify composite patterns in industrial wafermaps.
Power your factory with Spotfire
What are you waiting for? The factory of the future is here today with Spotfire. Get started collaborating across your enterprise, discovering the unknown, and measuring meaningful business outcomes.
Want to learn more about how Spotfire empowers manufacturing leaders like you? Check out our solution page to discover more.