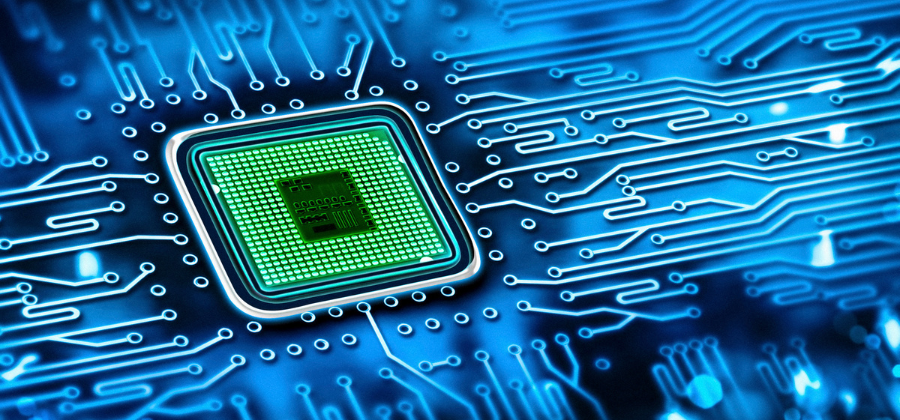
Key takeaways
- Hemlock Semiconductor unlocked siloed data and transformed operations across its enterprise.
- Spotfire enables predictive analytics, real-time decision-making, and agile responses to manufacturing challenges.
- Business and technical teams now collaborate seamlessly with a single source of data truth.
- What began as a solution for quality control became a catalyst for digital transformation.
Turning data overload into opportunity
Hemlock Semiconductor (HSC)—the largest U.S. producer of hyper-pure polysilicon—offers a compelling data visualization success story, using Spotfire® visual data science to turn massive, messy data into smart, sustainable decision-making.
Before its digital transformation, HSC was drowning in data. Every function, from manufacturing to finance, was generating massive volumes of information. But silos, inconsistencies, and outdated tools meant that this data went largely untapped. Despite being mission-critical, analytics lagged behind operational needs, leaving the company vulnerable to inefficiencies and missed opportunities.
Polysilicon is a material at the heart of semiconductors and solar technology, demanding absolute precision. But legacy systems could barely scratch the surface. Fragmented data access and limited historical analysis made it nearly impossible to uncover trends or optimize processes. The results? Inflexible reporting, duplicated efforts, and an inability to predict manufacturing outcomes in real time.
The challenge: Disconnected data and rising complexity
Hemlock Semiconductor’s initial hurdles were familiar to many manufacturers:
- Data silos and inconsistencies hindered access to insights.
- Reporting tools only supported 90 days of data—nowhere near enough for long-term trend analysis.
- Manual, spreadsheet-based analysis caused delays and inaccuracies.
- A backlog of IT requests slowed down decision-making.
- Real-time monitoring and predictive capabilities were not utilized.
In short, Hemlock had the data but not the tools to turn it into actionable insight.
Spotfire as the game changer
HSC turned to Spotfire, the visual data science platform that combines interactive dashboards with advanced analytics, streaming capabilities, and AI-powered recommendations. This was more than a software upgrade; it was a mindset shift.
Spotfire capabilities gave HSC a real-time window into processes that had previously been sealed black boxes. Engineers, scientists, and business users could now visualize complex operations, run predictive models, and automate decision-making—all without needing advanced coding skills.
With Spotfire, Hemlock Semiconductor:
- Unified data insights across manufacturing, supply chain, and finance.
- Enabled real-time and historical analysis for deeper insights.
- Applied machine learning to proactively optimize process control.
- Empowered non-technical users with intuitive drag-and-drop interfaces.
- Achieved centralized analytics without adding extensive tools or systems.
What success looks like: Measurable transformation
HSC’s journey with Spotfire didn’t stop at visibility; it led to continuous innovation. Here’s how the company transformed specific operations:
Cost of quality
By combining lab, ERP, and financial data, Hemlock created a consolidated view of quality costs. What used to take weeks to analyze now happens in hours, enabling predictive trend analysis and immediate corrective action. This has reduced variability—a major enemy of quality—and delivered significant cost savings.
Energy efficiency
Using Spotfire for supplier and process optimization, Hemlock saved approximately $300,000 monthly in energy costs, helping its utility partners reduce peak power loads.
Portfolio management
Spotfire enabled real-time visibility into $150M+ of project initiatives. Program sponsors and resource planners can spot delays or issues early before they become costly.
Process alerting
Automation in Spotfire flags any deviation from optimal manufacturing parameters in real time. The result? Faster issue resolution, better first-pass yield, and increased agility.
360-degree site operations
Using geoanalytics, engineers visualize real-time performance across HSC’s 200-acre facility. This bird’s-eye view allows them to drill into specific equipment or regions, speeding up troubleshooting and improving uptime.
Testing plan optimization
By applying machine learning, Hemlock minimized unnecessary lab tests while maximizing product quality. This streamlined its testing process and boosted lab capacity.
Before Spotfire | After Spotfire |
---|---|
Siloed systems with disconnected data | Unified data ecosystem spanning finance, ops, and lab systems |
Limited to 90 days of historical data | Multiyear historical and real-time analysis for trend prediction |
Manual spreadsheets delayed decision-making | Automated, real-time dashboards with predictive capabilities |
Weeks to analyze cost of quality | Insights delivered in hours—across financial, lab, and ERP data |
No visibility into live process conditions | Real-time alerting with Spotfire® Automation Services |
Missed energy optimization opportunities | $300K/month in energy savings using data-driven power management |
No site-wide asset tracking | 360-degree geoanalytics view of entire 200-acre manufacturing facility |
Lessons for other organizations
Hemlock Semiconductor’s success isn’t just a one-off win. It’s a blueprint. Here’s how others can follow suit:
- Start with strategic use cases: Target high-impact areas like quality control, cost optimization, or supply chain visibility.
- Leverage existing data sources: Use built-in connectors in Spotfire and data-wrangling tools to integrate everything from ERP systems to IoT sensors.
- Empower your team: With a visual-first interface, non-coders can extract insights and build dashboards without waiting on IT.
- Think iteratively: HSC scaled gradually by validating results, then expanding into new domains like energy, sustainability, and site operations.
Ready to see the power of visual data science in action?
Hemlock Semiconductor modernized its analytics and redefined operational excellence in high-tech manufacturing. With Spotfire, the company turned overwhelming data into precise, predictive, real-time insight that touches every corner of the business—from quality and energy savings to supply chain and site operations.
What could your team achieve with that kind of visibility and intelligence? If you’re facing challenges with siloed systems, slow reporting cycles, or limited insight into your data, HSC’s success story proves there’s a smarter way forward.
Download the full case study to learn more. Whether you’re a data leader, engineer, or operations exec, you’ll walk away with actionable ideas on how to put your data to work faster and smarter.